Colours & Coatings
Colours add personality and character to your building. We present you the main colour palette of Technopanel
* Special colours on request
- The described colours should be interpreted as approximate
- No guarantee for identic color shades on partial or additional deliveries due to the possibility of using different coils. In order to avoid nuance differences, complete information should be provided when ordering.
- Larger shade differences are possible with PVDF coatings
- Additional panels in reserve should be calculated when ordering specific colours
- Large temperature differences may occur between the internal and the sun exposed external sheet of the sandwich panels. As a result of the high coefficient of thermal expansion of the sheet, bending and tension stresses can be obtained in the cross-section of the panels. Special attention should be paid in this direction for colours of II and III colour group, and particularly for sandwich panels with PIR insulation core.
- Colour groups are defined according to EN 14509
Metal sheet Coatings Comparison
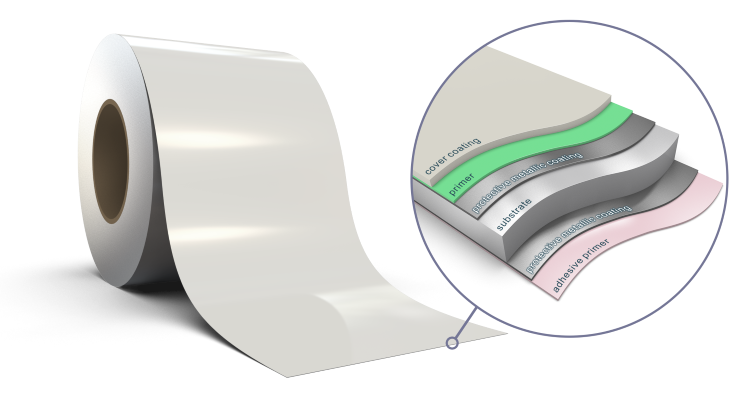
Resistance / Type of coating | Polyester PE | PVDF | PVC | Special coating *on request |
---|---|---|---|---|
Bending resistance | 3 | 4,5 | 5 | 3,5 |
Surface hardness | 4 | 3 | 2 | 5 |
Chemical resistance | 3 | 4,5 | 5 | 5 |
Humidity resistance | 3 | 4,5 | 4,5 | 5 |
Corrosion resistance | 3 | 4,5 | 4,5 | 5 |
Colour and gloss stability | 3 | 5 | 2 | 5 |
Environmental conditions / Type of coating | Polyester PE | PVDF | PVC | Special coating *on request |
---|---|---|---|---|
![]() |
![]() |
![]() |
![]() |
![]() |
![]() ![]() ![]() |
![]() |
![]() |
![]() |
![]() |
![]() ![]() |
![]() |
![]() |
![]() |
![]() |
![]() ![]() |
![]() |
![]() |
![]() |
![]() |
![]() ![]() |
![]() |
![]() |
![]() |
![]() |
![]() ![]() |
![]() |
![]() |
![]() |
![]() |
![]() |
![]() |
![]() |
![]() |
![]() |
![]() |
Handling, storage and assembly of sandwich panels
Packaging, Transport and Unloading
- maximal weight per pack – 2150 kg
- maximal pack length – 16000 mm
- maximal pack width – 1200 mm
- maximal pack heigh – 1200 mm
Name | sqm per truck *Lpanels = 13.5m | Pieces per pack | Packs per truck | Pieces per truck | Height per pack, mm |
---|---|---|---|---|---|
TFACE PU 25 | 2160 | 16 | 10 | 160 | 480 |
TFACE PU 30 | 1755 | 13 | 10 | 130 | 470 |
TFACE PU 40 | 1404 | 13 | 8 | 104 | 600 |
TFACE PU 50 | 1134 | 14 | 6 | 84 | 780 |
TFACE PU 60 | 972 | 12 | 6 | 72 | 800 |
TFACE PU 80 | 729 | 9 | 6 | 54 | 800 |
TFACE PU 100 | 594 | 11 | 4 | 44 | 1180 |
TFACE PU 120 | 486 | 6 | 6 | 36 | 800 |
TFACE PU 140 | 432 | 8 | 4 | 32 | 1200 |
TFACE PU 150 | 405 | 5 | 6 | 30 | 830 |
TFACE PU 160 | 378 | 7 | 4 | 28 | 1200 |
TFACE PU 180 | 324 | 6 | 4 | 24 | 1160 |
TFACE PU 200 | 270 | 5 | 4 | 20 | 1080 |
TTOP PU 30 | 1134 | 14 | 6 | 84 | 780 |
TTOP PU 40 | 972 | 12 | 6 | 72 | 800 |
TTOP PU 50 | 864 | 16 | 4 | 64 | 1200 |
TTOP PU 60 | 756 | 14 | 4 | 56 | 1200 |
TTOP PU 80 | 540 | 10 | 4 | 40 | 1080 |
TTOP PU 100 | 486 | 6 | 6 | 36 | 800 |
TTOP PU 120 | 432 | 8 | 4 | 32 | 1200 |
TTOP PU 160 | 324 | 6 | 4 | 24 | 1160 |
TFACE MW 50 | 1080 | 10 | 8 | 80 | 580 |
TFACE MW 60 | 864 | 8 | 8 | 64 | 560 |
TFACE MW 80 | 729 | 9 | 6 | 54 | 800 |
TFACE MW 100 | 567 | 7 | 6 | 42 | 780 |
TFACE MW 120 | 486 | 6 | 6 | 36 | 800 |
TFACE MW 140 | 432 | 8 | 4 | 32 | 1200 |
TFACE MW 150 | 405 | 5 | 6 | 30 | 830 |
TFACE MW 160 | 378 | 7 | 4 | 28 | 1200 |
TFACE MW 180 | 324 | 6 | 4 | 24 | 1160 |
TFACE MW 200 | 270 | 5 | 4 | 20 | 1080 |
TTOP MW 50 | 810 | 10 | 6 | 60 | 780 |
TTOP MW 60 | 648 | 8 | 6 | 48 | 720 |
TTOP MW 80 | 486 | 6 | 6 | 36 | 680 |
TTOP MW 100 | 486 | 6 | 6 | 36 | 800 |
TTOP MW 120 | 405 | 5 | 6 | 30 | 800 |
TTOP MW 160 | 324 | 6 | 4 | 24 | 1160 |
The vehicle to carry the panels should be equipped with cargo straps to ensure the cargo on the vehicle bed. Protective angular elements should be installed at the cargo straps to protect the edges of the panels. In case of flashing packages are being transported with the panel packages, they should be fastened separately.
If the stack is long particular attention should be paid to the bending and deflection. These problems are eliminated with the use of a crane beams and sleepers.
Stacks up to 6m can be raised and forklifts.Packets with length of 6m to 13,5 m should be lifted by crane or with forklift for long panels. To ensure protection of the edges of the panel in loading and unloading activities carried out by crane with lifting belts, stacks need to be reinforced at the bottom and at the top with protective angular elements that accompany the panels in each expedition.
Storage considerations
Do not keep the package of panels at a job site or warehouse more than 3 months. Put the packages with 5% slope, in order to prevent the water collection between the panels! Do not store more than three packages one on top of another and place spacers or board between them!
Instalation guidelines
During the installation of the panels there are often trimming operations on site needed. In those cases the following must be taken into account:
- During the cutting procedure, the panels must be laid horizontally and must be well supported on a workbench or on level supports with a soft surface (e.g. a wooden palette with polystyrene pieces, etc.
- Openings cut in roof and wall components, before the panel is assembled, weaken its cross-sectional structure, therefore adequate stiffening should be provided in those places.
- The cutting of roof covering materials is also possible when they have already been fixed in their final position on the metal frame of the building. In this case, make sure that they are firmly in place and not liable to wobble as they are being cut.
- If the panel is thick and it is difficult to cut the outer steel sheet and the inner aluminum/paper sheet of the panel at the same time, then the cutting line must be marked on both metal sheets so that the cutting can be carried out in two steps.
- During the installation often are formed clippings and/ or filings as a result of cutting the panel or using self-drilling screws. If they are not removed promptly from the panel surface they will corrode and cause rust staining, which is undesirable especially if the paint color is bright.
- The cutting tools must make the cutting clean and easy and must not damage the panel surface. For this reason, it is suggested that the cutting be done using a disk saw rather than a cutting wheel, with suitable guides for the best cutting line. Moreover, the disk saws must be of high quality to avoid damage to the cutting surface.
Use manufacturer recommended self-drilling fasteners for fixing the sandwich panels. The fastener type will depend upon the load carrying and the thickness of the panel being assembled.
In order to achieve adequate fastening of the panel to the structure it is essential to maintain perpendicular fastener position while fixing.
Use stainless steel fasteners for fixing panels to structures where the following conditions are preset:- The atmosphere inside is characterized by a permanent moisture content of above 70%.
- Chemically aggressive atmosphere is present inside.
- The equipment stored requires particular protection.
For panels with through fixing or / and when cutting panels on the site is needed, the recommended minimum distance of the screw from the end of the panel is 3-4 cm.
Roofing, Overlapping and Natural roof lighting with Polycarbonates
To prevent water ponding you should comply with the requirements for a minimum gradient of the slope as follows:
- min 7% (40) - for roofs of continuous panels without transverse joining and skylights.
- min 10% (5.70) - for roofs of joint panels or with skylights.
When overlapping is required or there is a low slope roof and / or for better water withdrawal at the roof, Technopanel offers a factory cut of the panels of 70 to 250 mm.
Policarbonates are an excellent material for the realization of natural roof lighting. Corrugated polycarbonates are mounted starting from the ridge. To ensure water impermeability of the connection with the gutter, it's reccomendet for the policarbonate at the bottom of the roof to overlap the sandwich panel. The overlapping of a polycarbonate panel on a sandwich panel is handled the same way as the overlap between two sandwich panels, with two rows of insulation gasket.
The polycarbonates are pre-drilled and the opening must be slightly wider than the screw to allow free movement due to thermal expansion. The use of callots is mandatory.
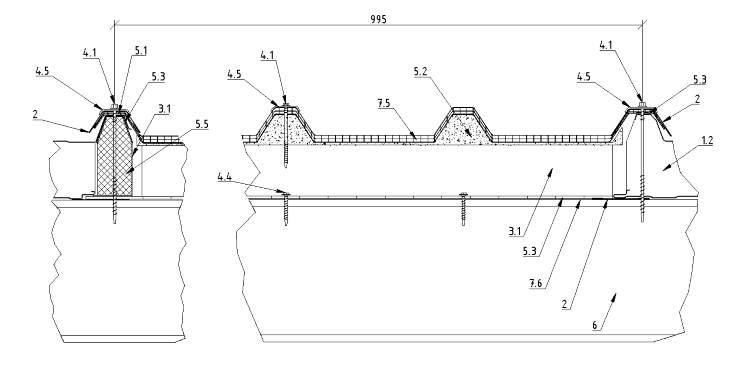